The Magic Formula for Improving Operational Effectiveness
Kevin Blais, Q-mation
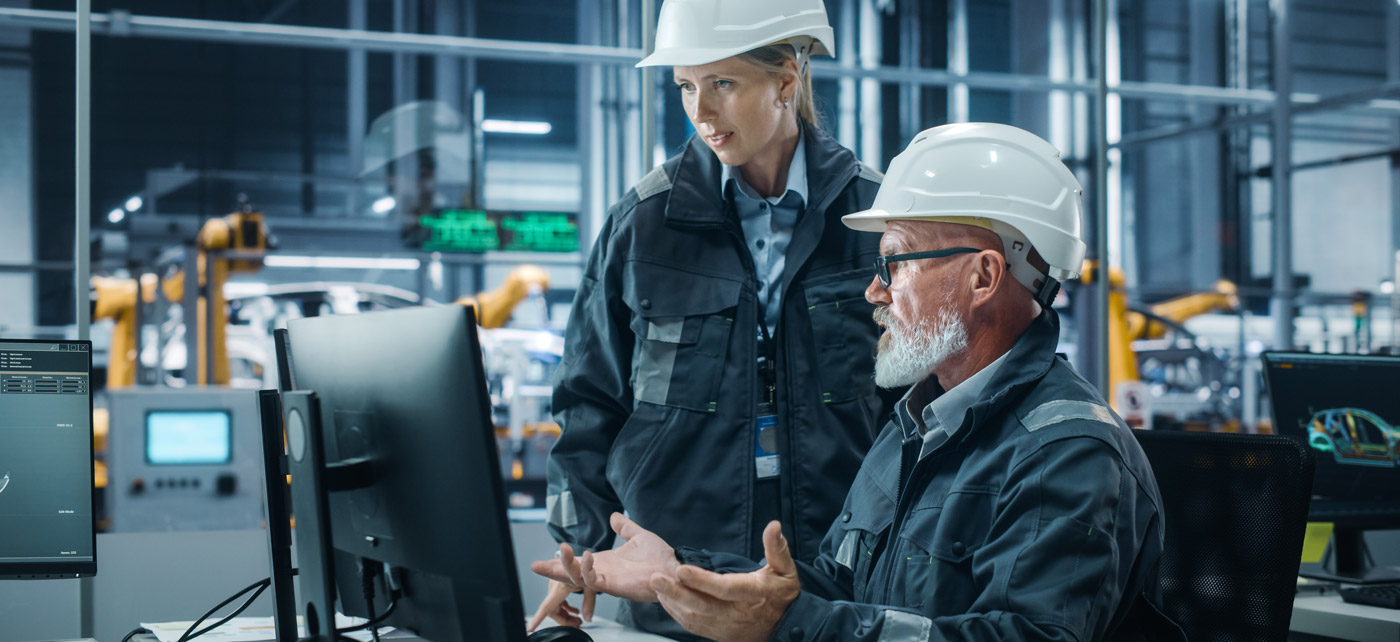
There was a time when a plant manager or maintenance manager could walk through a factory and determine the “health” of the operation by listening. It’s true. They would become so familiar with the equipment’s harmony that they could identify potential issues by simply listening. More importantly, they could quickly recall from last time what was required to address the issue disrupting the balance. For the most part, those days are gone. Today, factories have far more equipment, dynamic operations, and employee turnover. So, while the days of “tuning” factories by listening may be behind us, we are fortunate today to have many tools at our disposal to make the process more efficient.
Since the first Windows-based PCs were deployed to the plant floor, the ease of use and functionality of AVEVA products have led the industry. Never content to merely maintain a market leadership position, AVEVA has continued expanding its offering to deliver the most comprehensive set of products for industrial engineering, operations, and data management. As a result, never before have there been so many options for our customers to improve their operations through on-site or cloud-based solutions, including:
- HMIs to optimize the interaction between operator and machine
- Historians to collect and store massive amounts of process data and alarms
- MES software to help maintain order, effectiveness, and quality in operations
- Data Management software to contextualize, visualize and share critical industrial data
- EAM software to maintain and control operational assets and equipment
These are just a few of the many AVEVA offerings we provide our customers to help them build world-class manufacturing operations. These solutions focus on collecting data from key assets that is used to make critical operating decisions. Once properly installed and configured, these systems provide a platform for effective and efficient operations. But how do we capture the day-to-day operations and knowledge of our other vital assets: our people?
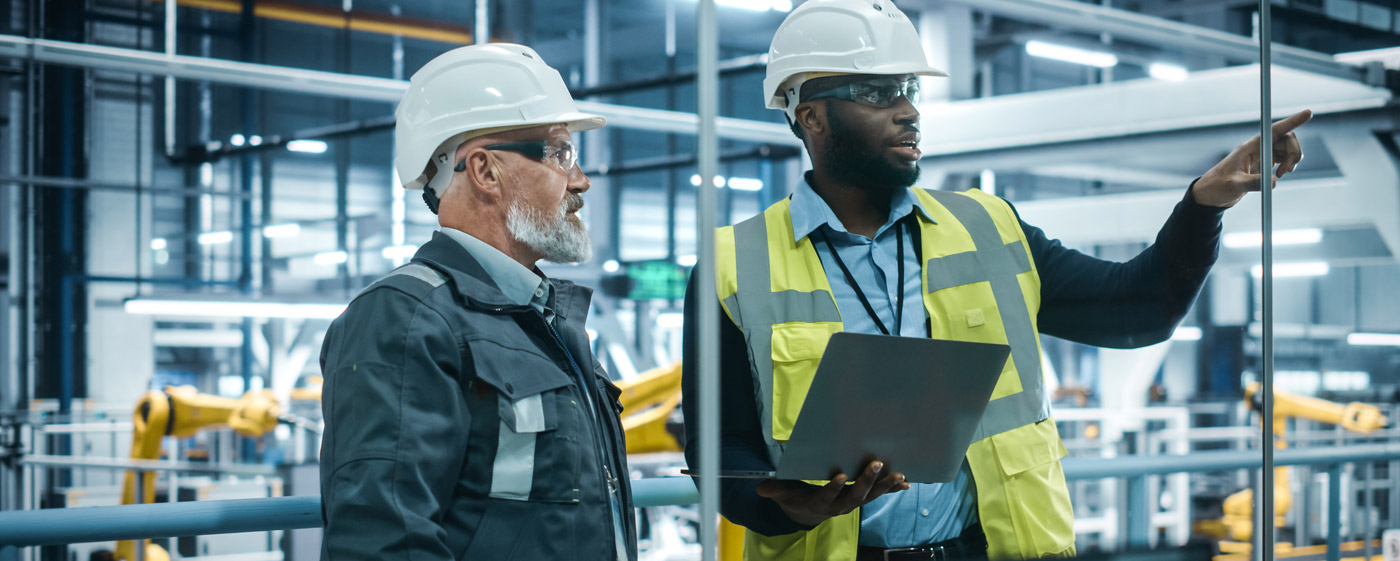
When an operational issue occurs on a product line, all of these components play a role in correcting the problem:
- Operators are notified of an issue by an HMI alarm
- The MES system alerts the operations team of production status
- Engineers use Historians and data management tools to determine the cause of the problem
- The EAM system schedules the appropriate action to take on the equipment
These systems all work to reduce unplanned downtime most effectively. But who is coordinating all the people from these cross-functional teams?
That’s where AVEVA Teamwork shines as the leading connected worker platform for driving manufacturing excellence. AVEVA Teamwork simplifies collaboration in real-time by providing a cloud-based knowledge and communications platform for the entire factory. Teamwork allows us to capture a storyboard of the incident response, including texts, pictures, videos, links, and documentation to inform the entire cross-functional team. In addition, key stakeholders can monitor the team’s progress to provide additional assistance and resources to produce the most effective solution. Teams can then review the storyboard of the incident and incorporate a best practices approach for future incidents.
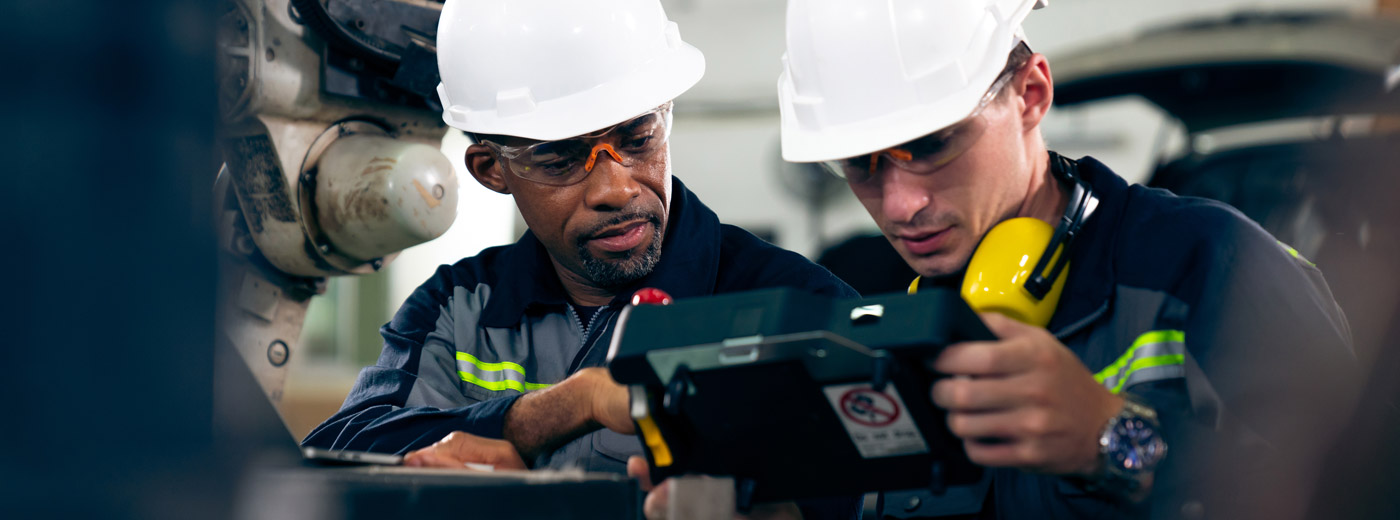
And just as we can create a “golden batch” for an optimal process outcome, we can now create a golden rule for an optimal set of work tasks. While this is a simplified example of a very powerful platform, our customers have successfully leveraged this technology to operate critical manufacturing assets efficiently. Using AVEVA Teamwork, we can leverage this technology to tap into the knowledge and power of people to provide efficient onboarding and rapid reaction to future events using best practices.
Are you ready to see how Q-mation and AVEVA Teamwork can connect your team to effectively collaborate and solve problems more efficiently? We can help!